AAC blocks are renowned for their lightweight, insulating, and load-bearing properties, making them a preferred choice in modern construction. This article delves into the manufacturing process of AAC blocks, including the raw material ratio, sizes, prices, and the remarkable properties that make them stand out in the construction landscape.
Wanna import AAC block from Iran to your country? We are here to help
leave your number and we will contact you shortly.
AAC Block Materials
Manufacturing process of AAC blocks and the production begins with precise formulation and mixing of raw materials. If you want to know what is AAC block,the key ingredients include sand, cement, lime, aluminum powder, and water.
- Sand: Sand is a primary component of AAC blocks and typically makes up a significant portion of the mixture. It provides the bulk of the material and helps to give AAC blocks their structural integrity.
- Cement: Portland cement is used as a binding agent in the AAC block mixture. It binds the sand particles together and contributes to the overall strength of the blocks.
- Lime: Lime is another essential ingredient in AAC production. It reacts with the aluminum powder to form calcium silicate hydrate, which gives the blocks their unique cellular structure. Lime also contributes to the blocks’ strength and durability.
- Aluminum Powder: Aluminum powder is a key ingredient that creates the aerated or cellular structure of AAC blocks. When aluminum powder is mixed with the other ingredients and exposed to water, it reacts to release hydrogen gas, which forms small air bubbles throughout the mixture. These air bubbles make the blocks lightweight and provide insulation properties.
- Water: Water is necessary to trigger the chemical reactions that result in the formation of hydrogen gas and the subsequent expansion of the mixture. It is used in the mixing process and also plays a role in the curing of AAC blocks.
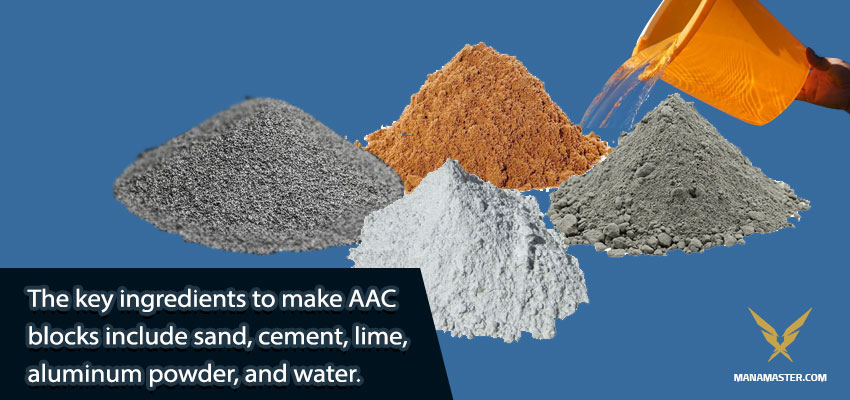
AAC Block Raw Material Ratio
In manufacturing process of AAC blocks, the raw material ratio is crucial, as it directly influences the quality and characteristics of the final product. While proportions may vary slightly depending on manufacturer specifications, a typical mixture might include:
- Sand: 60-70% by weight
- Cement: 20-30% by weight
- Lime: 5-15% by weight
- Aluminum powder: 0.05-0.2% by weight
- Water: Sufficient to create a slurry
The exact proportions are adjusted to achieve the desired density, strength, and insulation properties. Precise control of the mix ensures consistent product quality.
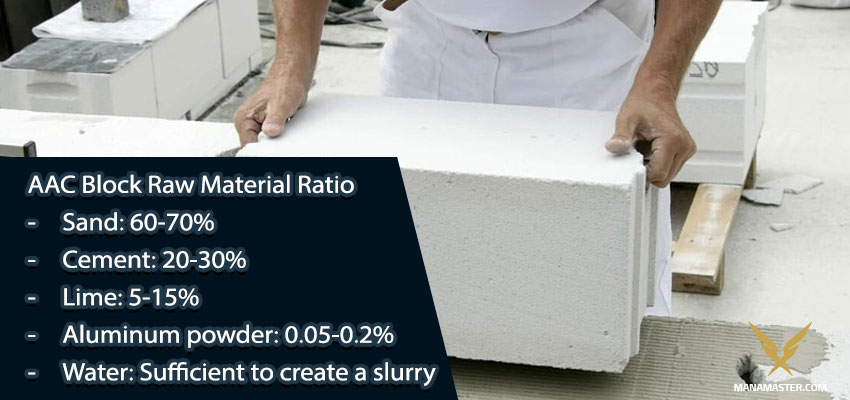
AAC Block Sizes and Prices
Manufacturing process of AAC blocks are popular because AAC blocks are available in a variety of sizes and shapes to suit different construction needs. Common sizes include standard blocks, larger structural blocks, and specialty blocks for specific applications. The prices of AAC blocks can vary depending on factors such as block size, density, and regional availability.
Generally, AAC blocks are competitively priced, considering their energy efficiency, durability, and other benefits. It’s advisable to obtain quotes from local suppliers to get a precise idea of pricing in your area.
Standard Blocks: These are the most commonly used AAC blocks for general construction purposes. They are available in various sizes, including:
- 200 mm x 75 mm x 600 mm
- 200 mm x 100 mm x 600 mm
- 200 mm x 150 mm x 600 mm
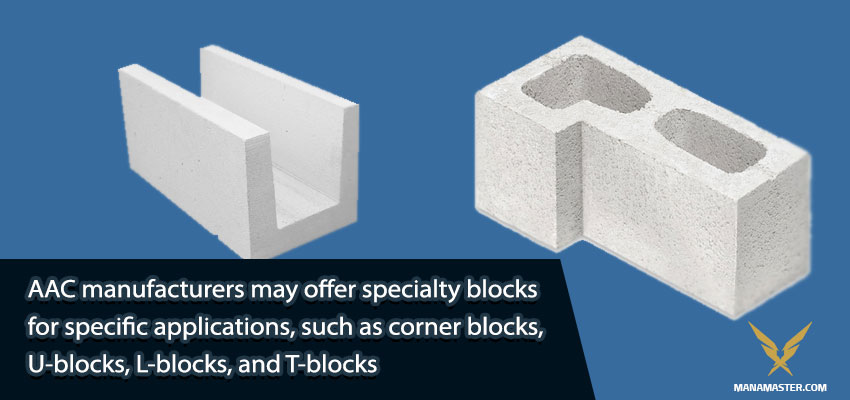
Large Blocks: These are typically used for structural elements and larger walls, offering more insulation and strength. Common sizes include:
- 200 mm x 200 mm x 600 mm
- 250 mm x 200 mm x 600 mm
- 300 mm x 200 mm x 600 mm
Specialty Blocks: AAC manufacturers may offer specialty blocks for specific applications, such as corner blocks, U-blocks, L-blocks, and T-blocks. These blocks cater to unique construction requirements.
AAC Block Prices:
AAC block prices can vary based on factors such as block size, density, location, and the specific manufacturer or supplier.
To get the updated price of AAC blocks, call Manalex today.
How to Make AAC Blocks: Manufacturing process of AAC blocks
The manufacturing process of AAC blocks involves several key steps:
- Mixing: The raw materials are mixed in precise proportions to create a slurry or paste. The mixture includes sand, cement, lime, and aluminum powder. Water is added to initiate the chemical reactions.
- Pouring into Molds: The slurry is poured into molds of various sizes and shapes. The molds may have a reinforcing mesh or steel reinforcement for added strength.
- Curing: The filled molds are placed in an autoclave, a high-pressure steam chamber. Here, the mixture undergoes curing at elevated temperatures and pressure. The steam-curing process triggers chemical reactions, resulting in the formation of hydrogen gas, which creates the characteristic air bubbles in the blocks.
- Cutting and Shaping: After curing, the blocks are removed from the molds and cut into their final sizes using wire cutting machines. They may also be shaped or modified as needed.
- Quality Control: The finished blocks undergo quality checks for strength, density, and other properties to ensure they meet industry standards.
- read more: Iranian AAC blocks export
Conclusion
The manufacturing process of AAC blocks, from the precise raw material ratio to the curing process, plays a pivotal role in creating a construction material with exceptional properties. As the construction industry continues to evolve, AAC blocks are poised to play a significant role in shaping the buildings of the future.
Hi. I just left my number. hope to get a call soon
Our sales team at Manablock will contact you shortly
Do you supply all the sizes you mentioned in the article?
Hi. The sizes we provide are:
600mm * 240mm * 200mm
600mm * 240mm * 80mm
600mm * 240mm * 120mm
600mm * 240mm * 200mm
600mm * 240mm * 100mm
600mm * 240mm * 150mm